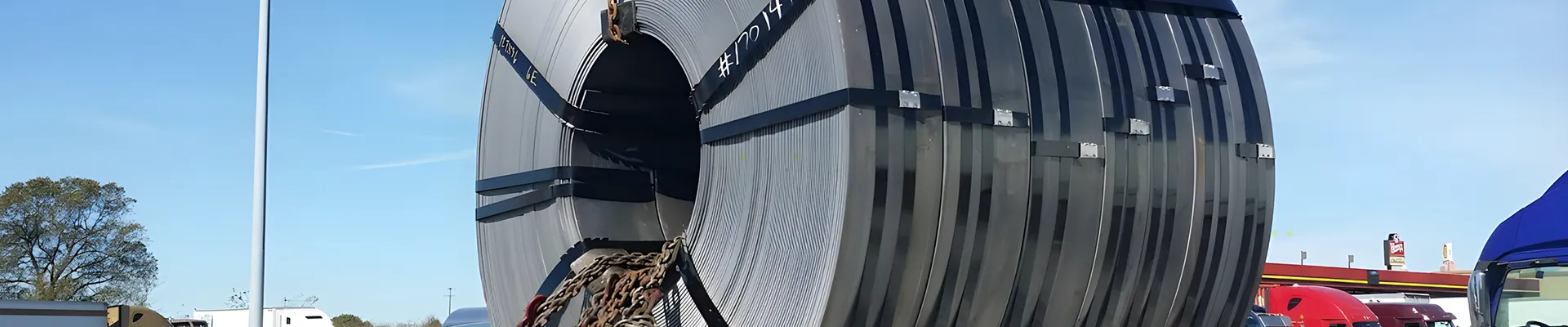
A Guide to Selecting the Right Steel for Building Humanoid Robots
release time:
2025-04-10 13:30
source:
Choosing steel suitable for humanoid robot manufacturing requires comprehensive consideration of multiple factors. Here are some key points:
Strength and rigidity: Humanoid robots will be subjected to various forces and torques during movement, so the steel needs to have sufficient strength and rigidity to ensure the structural stability of the robot and prevent deformation and damage. For example, high-strength alloy steels, such as chromium-molybdenum alloy steels, can be used in the joints and load-bearing parts of the robot. They have high yield strength and tensile strength and can meet the structural requirements of the robot under complex movements and loads.
Lightweight: In order to improve the movement flexibility and efficiency of the robot, it is important to reduce its own weight. Under the premise of ensuring strength, steels with relatively low density, such as high-strength aluminum alloy steels or titanium-containing alloy steels, should be selected. These steels can still provide good mechanical properties while reducing weight.
Wear resistance: Some parts of the robot, such as joint shafts, gears, etc., will wear during long-term movement, so steels need to have good wear resistance to extend the service life of the robot. High carbon chromium bearing steel is a commonly used wear-resistant steel with high hardness, high strength and good wear resistance. It is suitable for manufacturing robot joint shafts and gears and other easily worn parts.
Corrosion resistance: If the robot needs to work in a corrosive environment such as moisture, acid and alkali, then the corrosion resistance of the steel is crucial. Stainless steel is an ideal choice, such as 304 stainless steel or 316 stainless steel, which have good corrosion resistance and oxidation resistance, can maintain stable performance in harsh environments, and prevent rust and corrosion.
Processing performance: The processing performance of steel directly affects the manufacturing process and cost of the robot. Easy-to-process steel can reduce manufacturing difficulty and cost and improve production efficiency. For example, some low-carbon steel and medium-carbon steel have good cutting performance and forming performance, and are suitable for forging, stamping, cutting and other processing processes, which can easily manufacture robot parts of various complex shapes.
Weldability: In robot manufacturing, welding is one of the commonly used connection processes, so steel needs to have good weldability to ensure welding quality and connection strength. For parts that need to be welded, steel with good welding performance can be selected, such as low-alloy high-strength steel, which is not prone to defects such as cracks and pores during welding and can ensure the mechanical properties of the welded joint.
Cost: Cost is also an important consideration in selecting steel. On the premise of meeting the performance requirements of the robot, steel with lower costs should be selected as much as possible to control manufacturing costs. The prices of different types and specifications of steel vary greatly, and a comprehensive balance needs to be made based on the actual needs and budget of the robot. For example, for some non-critical components that do not have particularly high performance requirements, ordinary carbon steel or relatively low-alloy steel with relatively low prices can be used to reduce costs.